A type of cement that sets very quickly and hardens with the addition of water to the finely ground cement is called hydraulic cement. It is the most commonly used cement at present.
Nowadays, usually different blends of modern Portland cement are commercially referred to as hydraulic cement. Composed of hydraulic calcium silicates (generally containing calcium sulfate), hydraulic cement is a non-corrosive, non-rusting and non-shrink substance widely used in construction. This type of cement is especially good for structures that are constantly in contact with water because it is impermeable to water.
History and Development of Hydraulic Cement
Hydraulic cement was first used by the Romans in the middle ages when “hydraulic cement” was just volcanic ashes mixed with lime. In the 18th century, James Parker patented the Roman cement, which gained popularity but was replaced by Portland cement in the 1850s.
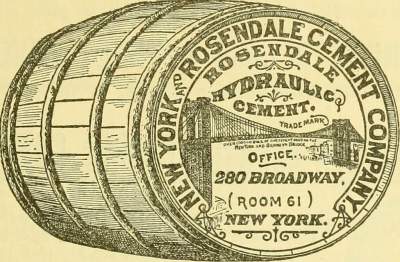
In the 19th century, Frenchman Louis Vicat laid the foundation for the chemical composition of Portland cement while in Russia, Egor Cheliev published the use, advantages, and methods of making cement. Joseph Aspdin brought Portland cement to the market in England and his son, William Aspdin, developed the “modern” Portland cement, which was soon in quite high demand.
But the real father of Portland cement is considered to be Isaac Charles Johnson, who contributed immensely to the development of hydraulic cement by publishing the process of developing meso-Portland cement in the kiln. Since then, hydraulic cement has gone through extensive development to be produced as the refined product seen today. Different blends of hydraulic cement are now available to suit the particular needs of a construction project.
Chemical Composition of Hydraulic Cement
The four main components of hydraulic cement are
- Belite (2CaO·SiO2)
- Alite (3CaO·SiO2)
- Tricalcium aluminate/ Celite (3CaO·Al2O3)
- Brownmillerite (4CaO·Al2O3·Fe2O3)
The mechanical properties of cement are given by the silicates (belite, alite) whereas the last two ingredients are required for the liquid phase in the production process inside the kiln. Certain additives are also needed for special properties such as greatly reduced setting and curing time, prevention of shrinking, being able to be used underwater etc. The exact chemistry of the reactions responsible for the production of cement is still a subject of research.
How Does Hydraulic Cement Works
Hydraulic cement’s working principle is based on the process of hydration, which means the product hardens when water is added. Certain substances present in hydraulic cement initiate reactions due to the application of water, causing the mixture to set and harden very quickly with reduced curing time. The nature of these chemical products makes hydraulic cement impervious to water damage and further chemical attacks. Hence, this type of cement is suitable for construction of structures in close contact with or submerged in water.
Another chief property of hydraulic cement is its strength. Tricalcium silicate and dicalcium silicate present in such type of cement undergo the following reactions upon addition of water:
Tricalcium silicate + water → calcium silicate hydrate + other chemical products
Dicalcium silicate + water → calcium silicate hydrate +other chemical products
The main product of these reactions, calcium silicate hydrate, has a network of short fibers that increases the strength of the product greatly, also making it water-tight. {adselite}
When to Use Hydraulic Cement
The right type of cement is to be selected based on the nature of the construction work. Different blends of hydraulic cement contain varying ratios of chemical components to suit specific needs.
Hydraulic cement is highly suitable for projects that require quick setting and less curing time. However, it only gives a short window of time to work with it before it hardens, so it is recommended to apply hydraulic cement only for projects that can be done in 10-15 mins with a moderate amount of cement mix prepared at a time.
Its ability to provide strength is immense, so hydraulic cement can be used for the construction of highly durable structures. The cement is not flexible, so it can only be used to provide mechanical support to structures.
For constructing underwater structures, hydraulic cement has almost no alternative. Being impermeable to water, it can be used in constructing structures that are in constant contact with water. This type of cement does not corrode or rust, hence it retains its strength even when submerged in water. It is also extremely useful for water-proofing.
If the construction requires high durability but the location is in an extremely cold climate or on a frozen surface, applying hydraulic cement is not commendable in such circumstances unless certain measures are taken to ensure durability.
Hydraulic cement does not shrink like normal cement, and some blends even expand upon hardening. This type expanding hydraulic cement is very useful for sealing concrete leaks and repair work. Sealing cracks with hydraulic cement will hold for many years, but it is not a permanent fix. For very fine cracks, caulk might be a better solution than hydraulic cement. Again, hydraulic cement will not solve problems caused due to condensation and not leaking.